Preventing Unplanned Downtime
When a motor-driven machine starts to fail, one of the earliest signs is an increase in power draw by that motor — typically well before you can hear a problem or before the motor overheats.
SiteWatch 360 has a simple, but effective, early-warning system to identify issues while they are still developing and alerting machine operators or management to the problem — in enough time to do something about it.
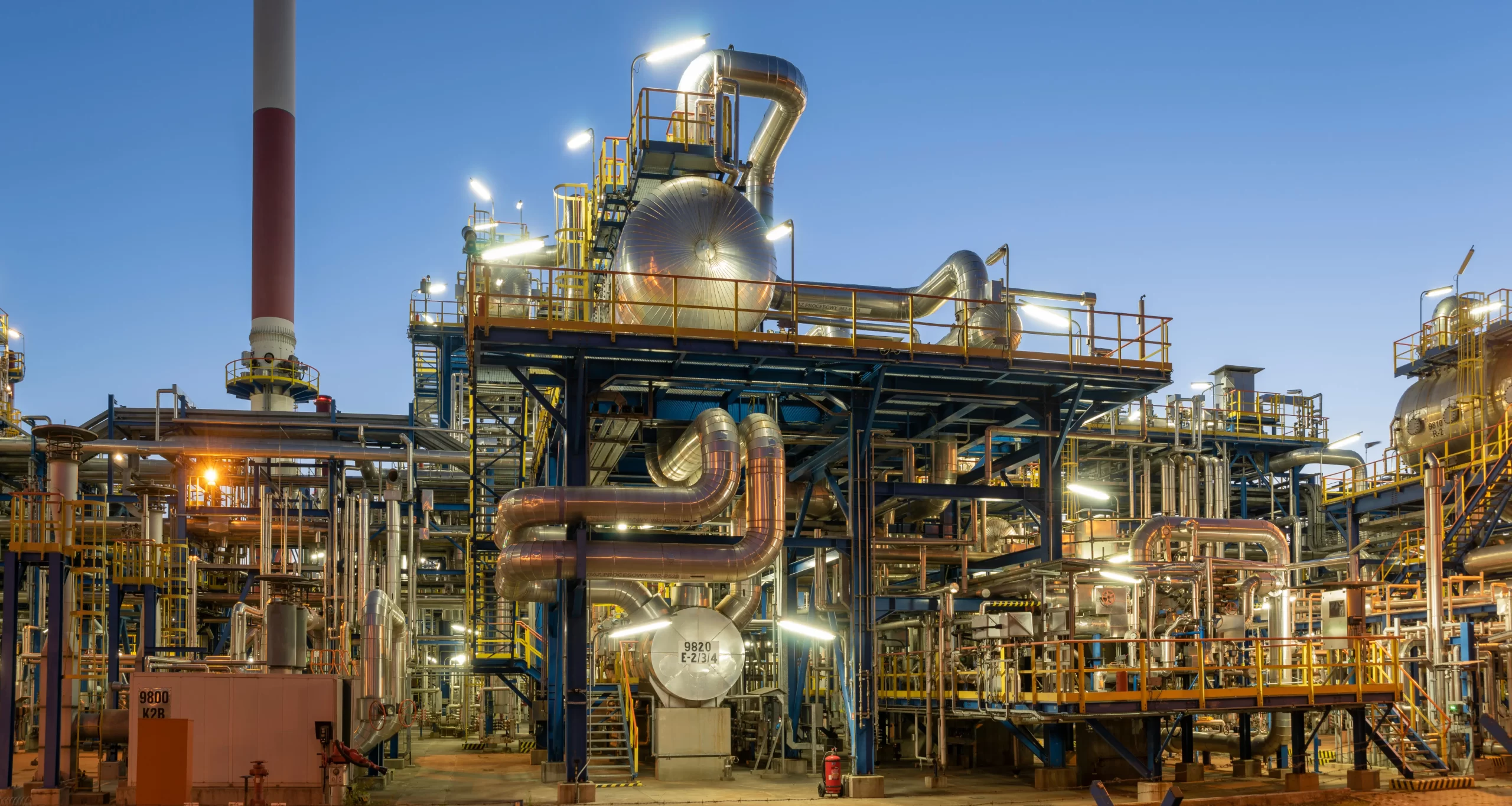
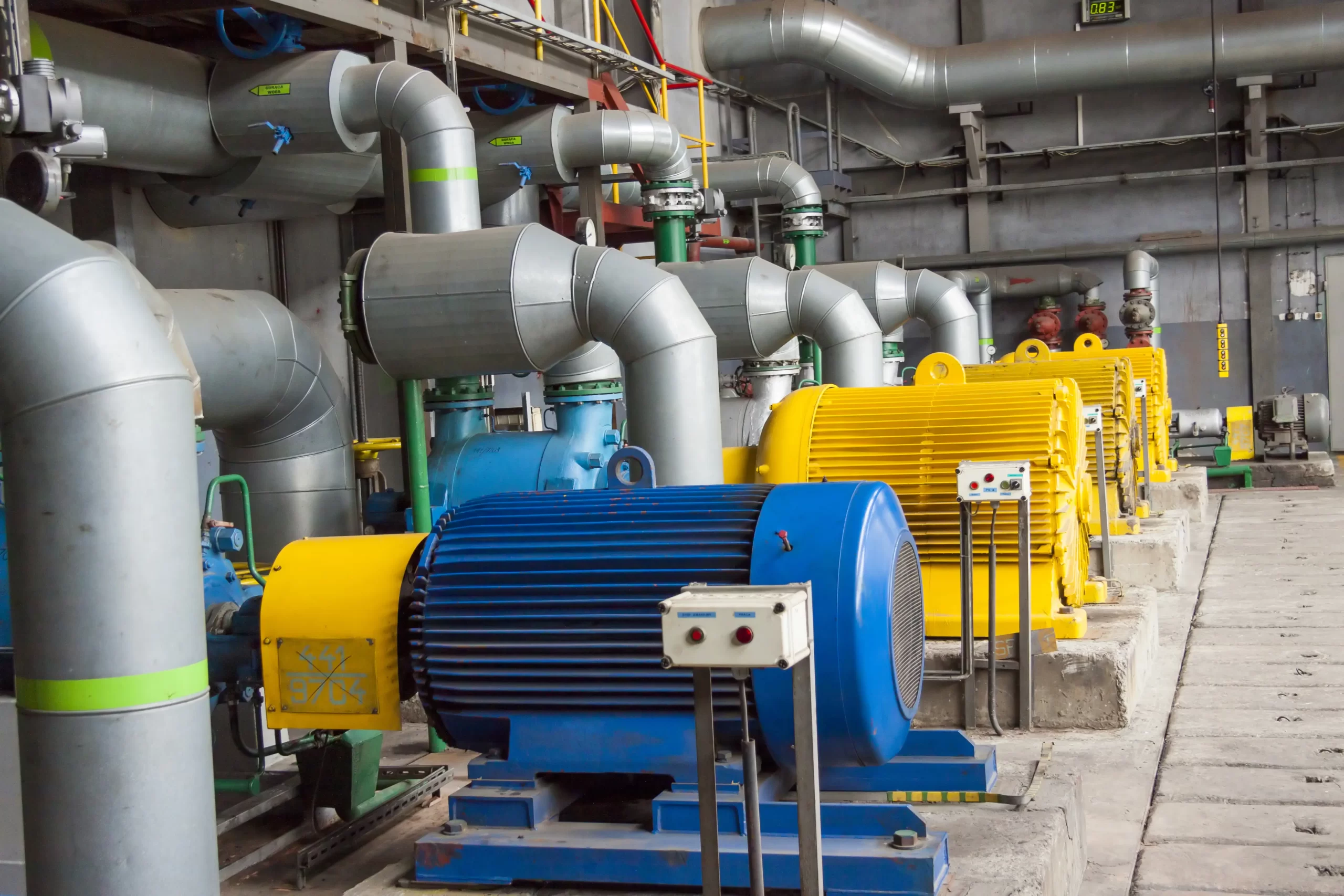
What Causes Equipment Failure?
Common causes of equipment failure can include…
- Overheating from torque overload
- Over-current
- Low Voltage
- Phase imbalance
- Broken drive belt
- Loose coupling
- Open pump discharge
- Clogged intake filter
The Cost of Equipment Failure
Whatever the cause, the cost of equipment failure is not just the replacement of a part or a motor. It's much broader and more serious than that.
Costs of failure can include…
- Replacing or rewinding motors.
- Labor for installation of parts.
- Production-downtime, often measured in thousands of dollars an hour.
- Missed customer deadlines since breakdowns always occur at the worst possible time (Murphy's Law).
- Spare parts, including shipping them in rapidly if not on hand.
- Flying in engineers/technicians to make complex repairs.
- Significant disruption of production schedules and management time solving the problem.
The good news is that SiteWatch's affordable system makes it extremely cost-effective to monitor critical equipment in real time, watching energy usage patterns for signs of impending machine failure.
Setting Failure Alerts
SiteWatch 360 has a simple, but effective, alerting system that will warns if a machine's health and performance have begun to deteriorate — for whatever reason — in enough time to address the problem before that machine fails catastrophically.
Alerts can be triggered in two ways…
- By a machine's power draw moving out of its “normal” range for a period of time that you can set — e.g. 30 seconds, 3 minutes, 3 hours or 3 days.
- By the length of time a machine is operating — too short or too long.
More complex multi-variable (compound) alerts are also possible. If several conditions are met — for a water-cooled chiller, for example — either one or more of these conditions — an increase in power-draw and/or a decrease in cooling-water volume and/or a high cooling-water temperature for a pre-set period of time — will result in an alert being sent to whoever is designated to respond.
Here are two examples of SiteWatch 360's alerts averting problems with furnaces:
A Furnace
The two graphs below show the operation of a furnace over two consecutive weeks — the first week is shown in orange and the second in blue. When the client was shown the orange graph he knew immediately that the furnace was ‘short-cycling’ probably due to a heater element failing — which puts more load on the remaining elements.
On Tuesday of the second week, the client shut the furnace down and replace two of the heating elements, then started up again the following day. Clearly the operating pattern changes substantially from then on to a much more energy-efficient pattern.
FAQ
How can I verify that a cost-saving initiative has, in fact, saved money?
SiteWatch 360 can provide detailed comparative energy cost data both before and after an energy efficiency project.
What is the easiest way to find out the cost of running a particular machine on different settings?
SiteWatch 360 will measure and report on energy use at each setting. Production data can be overlaid on this data.
How fast can I start monitoring 50-100 machines?
Installing SiteWatch 360 takes about 1 day on up to 50-100 machines, once someone selects which machines are to be monitored.
Can I avoid installing sub-meters on most of my equipment?
With SiteWatch 360's amperage sensors on individual circuits and our power meter on the system as a whole, there's no need to install hard-wired sub-meters, which take longer and cost considerably more.